The fate of labor in the era of great changes: (1) Unemployment and closed-loop production
Since the global financial crisis and the Sino-US trade war, China's manufacturing industry has faced many structural challenges such as the disappearance of the demographic dividend, the rising labor movement, and the increase in export tariffs, which has triggered a new round of global industrial transfer and a large number of labor-intensive industries. From China's Pearl River Delta region to Southeast Asian countries, this cost-sensitive supply chain restructuring is in line with the economic rationality of "race to the bottom" for transnational corporations. However, the outbreak of the new crown epidemic has fundamentally changed the logic of the vertical integration of global value division of labor in the past, because European and American countries have found that excessive dependence on Chinese-made goods will damage national security in times of major crisis, and on the issue of Russia's war of aggression against Ukraine, China remains neutral on the surface, but in fact, the position of "cooperating" with Russia highlights the risk that the supply chain is subject to China.
On the other hand, China has adopted "dynamic clearing" as a basic national policy of "can do, but can't say", and implement epidemic prevention measures from the height of "political accounts". Sex, large-scale lockdowns have become the norm. According to media reports, since late August, more than 300 million people in at least 74 cities in China have been under the lockdown of the whole city or some administrative regions and multiple communities. This kind of Don Quixote-style epidemic prevention system not only affects the normal life of residents and causes various humanitarian disasters, but also artificially interrupts the production and supply chain and seriously damages the economic foundation. Especially the long-term effects of Shanghai's closure are emerging. The parts supply chain is considering decoupling China from other regions, and Mazda also requires about 200 companies that deliver parts through China to transfer their inventories to Japan, and suggests that some parts suppliers produce at bases outside China at the same time.
The superposition of multiple international and domestic factors has caused China to shake its status as the "world factory" that has been time-consuming and labor-intensive since China's reform and opening up. This is a moment of great economic change. For multinational capital, for the past 25 years or so, their decision has been relatively easy, that is, as long as it is made in China. But now the situation has changed. Having multiple suppliers in China is not beneficial. They must pursue geographic diversity and accelerate the decoupling of supply chains in order to deal with the imminent campaign epidemic prevention and geopolitical risks. From the perspective of macro data, the Caixin China Manufacturing Purchasing Managers Index (PMI) recorded 49.5 in August, below the threshold of prosperity and decline, the new orders index and the new export order index both fell to the contraction range, and the output of consumer goods manufacturing declined.
Bankruptcy
The sluggish demand in the manufacturing industry is largely affected by the clearing and epidemic prevention system. Due to the difficulty of entry and exit of overseas customers, many orders have been lost, logistics closures have prevented many materials from being in place, production has been intermittent, and the cost of raw materials has risen, exporting enterprises The operation is getting more and more difficult, and the reduction of scale and even the suspension of production has become the new normal. In June this year, Dongguan Chuangdian Electronics Co., Ltd. announced that the company’s orders had decreased, and the payment was blocked, resulting in serious business difficulties. It had to stop production and production from June 27, 2022; in July, Dongguan Cooper Electronics was accepted by many cross-border e-commerce companies. The payment for the goods is in arrears, and a large number of finished products are accumulated in the warehouse, causing a vicious circle. The domestic and foreign orders are seriously disconnected, and they have fallen sharply. , a Shenzhen company issued a notice saying that in view of the current seriousness of the new crown epidemic and the impact of the global international trade situation, the company's order volume has been reduced and the production department's output has suddenly stopped, resulting in extremely difficult production and operation. Since July, overtime on Saturdays, Sundays and other days has been gradually reduced, and it is now decided to take a holiday from September 1, 2022 to December 31, 2022; in August, many companies with a long history and long-standing reputation in the foreign trade export industry The old-fashioned manufacturing enterprises of the company finally couldn't last after the suspension of production and business to no avail. On the 29th, Shenzhen Welima Electric Appliance Manufacturing Co., Ltd. and Fulong Electric Appliance Manufacturing Co., Ltd. issued an announcement announcing the early dissolution of the company. On the 31st, Dongguan Aigo Electric Co., Ltd. officially closed its business. These three are not ordinary export manufacturing enterprises, all of which have been established for more than 30 years, and were once the benchmark for export manufacturing enterprises. For example, Aigo Electronics Factory was the second largest factory in Houjie, Dongguan, with more than 10,000 workers in the 1990s.
Over the past decade or so, manufacturing enterprises in the Pearl River Delta have gone through several rounds of "bankruptcies". The causes are different, but they all have adverse effects on migrant workers without exception. In early 2009, Chen Xiwen, then director of the Office of the Central Leading Group for Rural Work, revealed that about 20 million migrant workers returned home because of the shutdown of export manufacturing enterprises. In contrast, the economic situation this year is more complex and changeable. The decoupling of supply chains, one-size-fits-all epidemic prevention, and high-temperature power rationing have made the structural impact on manufacturing companies far worse than the financial crisis, making economic recovery even more difficult and effective. Therefore, the impact on migrant workers will be long-term and painful.
wave of unemployment
A Dongguan company's "Notice of Suspension of Work, Production and Waiting for Work" states that the factory will officially suspend production and production from July 1, 2022, and will no longer provide jobs; For benefits such as accommodation, canteen conditions or room and board subsidies, the company pays a monthly living allowance equivalent to 80% of the minimum wage in Dongguan. The current minimum wage in Dongguan is 1,720 yuan per month, which means that during the shutdown period, workers only have 1,376 yuan per month, which is not enough to pay rent. In fact, this is a common method used by factories to force workers to leave their jobs to avoid severance compensation, and workers have to find another way to make a living. However, in an environment where the manufacturing industry is in recession as a whole, no matter which industry or factory they work in, migrant workers will encounter a series of difficulties, including but not limited to structural unemployment, deteriorating labor conditions, increasing income inequality, and labor-management conflicts. Increased and frequent protest movements.
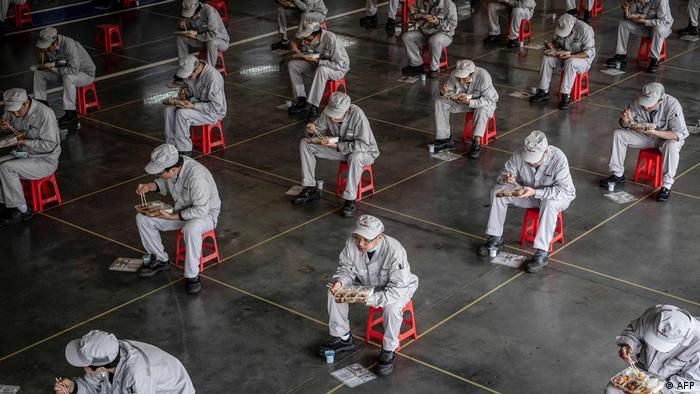
The National Bureau of Statistics announced in August that the unemployment rate of the national urban survey in July was 5.4%, of which the unemployment rate of the 16-24-year-old population reached an astonishing 19.9%, exceeding the level of the United States and the European Union, while the unemployment rate of the migrant household survey was 5.5%. Among them, the unemployment rate of migrants with agricultural household registration is 5.1%. This data partially reflects the unemployment problem of migrant workers, but the real situation will only get worse. In the past few years, the rapid development of the platform economy such as online car-hailing and express delivery has absorbed a considerable number of migrant workers who have been transferred from the recession of the manufacturing industry, especially Meituan. The data shows that during the epidemic this year, there were 580,000 new riders in two months. , of which 40% are manufacturing workers.
However, the employment absorption capacity of the platform economy is limited by the scale of consumption. After reaching a certain proportion, it is difficult to continue to grow. Moreover, with the sharp increase in the number of employees, the platform has greater market bargaining power to adjust the algorithm to promote competition, resulting in labor conditions. Deterioration and lower income levels are common problems faced by online car-hailing drivers and takeaway riders. They have to work more than ten hours to get three or four thousand yuan in income. Compared with manufacturing, platform labor is unstable employment and lacks social security. From this perspective, one of the consequences of the manufacturing recession is to promote the flexibility of the entire labor market. The majority of the 200 million people who are officially employed in flexible employment are still migrant workers.
closed loop production
In the era of great changes, even if manufacturing companies escaped the fate of bankruptcy, they still face many difficulties in resuming work and production under the epidemic, especially how to ensure that employee management meets the requirements of epidemic prevention. In April, Shanghai required resumption enterprises to conduct daily health monitoring and registration of all employees, and insist on two tests a day: antigen testing in the morning and nucleic acid testing in the evening. At the same time, implement physical isolation between areas, implement "two points and one line" management of workplaces and residences, all personnel work and live in designated positions, and minimize direct contact between personnel in different areas.
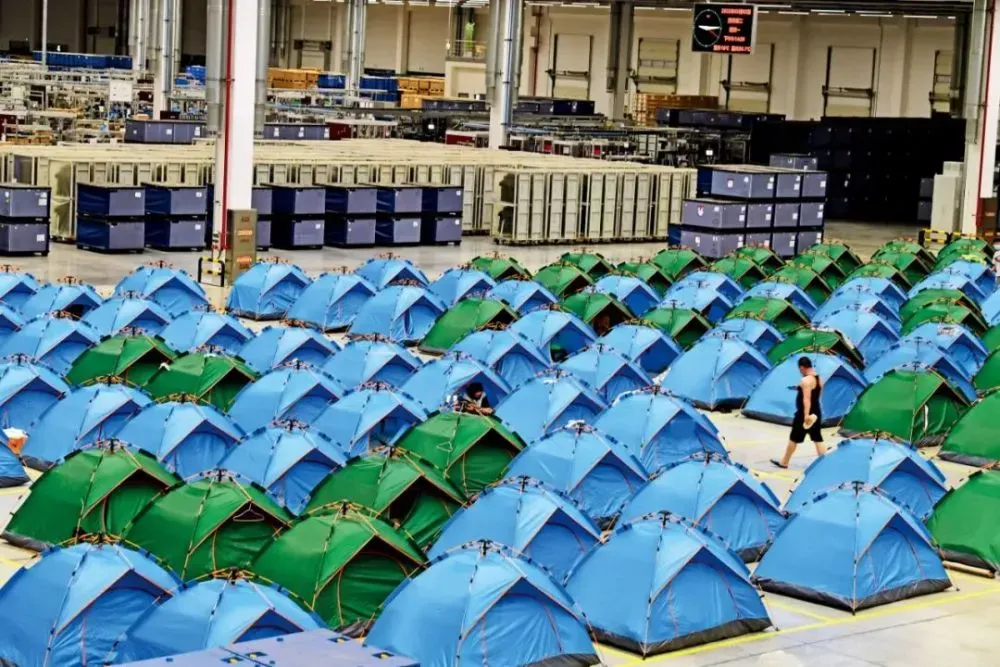
Such an approach is difficult to implement: the standards implemented by different administrative management units are different, especially the neighborhood committees at the end of the government management structure may not necessarily approve the labor demand certificate issued by the enterprise, because the political pressure on the neighborhood committees is based on Epidemic prevention is the first priority. As a result, the grass-roots management personnel in the community do not allow residents to go out, and the buses arranged by the company cannot take employees back to the factory. In addition, the procedures are complicated, the overall efficiency is low, and the employee's arrival rate is very low. Even if the employees are allowed to work, they cannot return to the place of residence and can only "take the factory as their home".
According to media reports, on March 14, SAIC Volkswagen started closed-loop management and arranged for more than 8,000 workers to eat and sleep in the factory. Some employees suddenly received overtime notices when they were about to leave work. To their surprise, half an hour in the original notice became directly closed in the factory for several weeks. SAIC has prepared camp beds, tents and yoga mats for the workers. At night, "everyone sleeps in neatly". During the closure period, everyone worked about 10 hours per shift. There are many practical challenges for employees to eat and live in factories, because most companies basically do not have complete infrastructure, such as a large enough canteen and enough dormitories, how to solve the problem of food and accommodation, bathing and leisure time. Making a floor, sleeping in a sleeping bag, and living in a tent have become the daily routine of thousands of Chinese workers.
Shanghai Ricoh Digital Equipment Co., Ltd. has placed a large number of containers in the factory area, and each container has six beds, and only distributes basic daily necessities and instant noodles and other basic foods to employees. Shanghai British-owned enterprise Nateford Transmission System Co., Ltd. implements the model of "fixed-point accommodation" outside the factory, conducts "closed" accommodation management for employees, and "point-to-point" special shuttle bus for commuting, that is, workers eat breakfast at the accommodation every day and finish their work. For preparations such as antigen testing, take the company shuttle bus to the factory. Each off-site accommodation site has a special person responsible for logistical support, and reports the occupancy situation, as well as antigen and nucleic acid test results to the company's management department on a daily basis. The security personnel report to the company the results of the inspection at the gate and work points every day to ensure that every entry and exit of personnel meets the requirements of epidemic prevention bubble management, which is the precondition for resumption of work and production.
Even for Chinese workers, sleeping in production workshops, tents, or shipping containers with cardboard as a mattress is not a normal way of life. The conditions were harsh, backache and leg pain were unavoidable, and the workers did not have any personal space of their own. In addition, many companies require employees to work overtime for free or increase their work intensity in order to recover the losses caused by the shutdown. For example, after the resumption of work, Tesla changed the production rhythm of the previous 8-hour shift system, allowing employees to work 12 hours a day, 6 days a week, and a day off. At the beginning of May, the FAW-Volkswagen Party Committee put forward the slogan of "fighting for 60 days and winning the first half of the year". In the case of normal production only half of the time from January to April, the production and sales target in 2022 will not be shaken. According to Yang Hai, Director of FAW-Volkswagen Production Management Department, "Since the beginning of May, more than 18,000 employees in Changchun Base have adopted measures such as closed-loop management, 15 days off for 1 day, and double shifts for 21 hours to fight back the losses caused by the epidemic." , the result is that in May, the base broke the historical record of production capacity for the first time.
This kind of high-intensity work certainly satisfies the pursuit of wealth by capital, but it also reflects the deterioration of labor conditions under the epidemic. In the long run, it will inevitably damage the physical and mental health of workers. On May 6 and 27, workers from Shanghai Quanta Computer rushed to the factory area to protest twice because of the strict closed-loop production management during the epidemic, and clashed with security personnel. In order to reduce the labor intensity of workers, the Shanghai Federation of Trade Unions requires no more than three hours of overtime per day, which reflects the terrible production pressure that workers are actually facing.
Nevertheless, under the closed-loop resumption of work, not only will the daily production capacity not keep up with the normal level, but no matter how strict the closed-loop management is, there will be loopholes, and enterprises have to face the sudden impact of the epidemic at any time. For example, Aptiv, the largest supplier of automotive wiring harnesses in China, is one of the first "whitelist" companies in Shanghai to resume production. Since March 31, more than 1,800 employees have entered closed-loop production, but employees reappeared one day after the factory in Jiading resumed work. Infection, it had to stop work again, resulting in blocked supply to Tesla, SAIC Volkswagen, Toyota and other vehicle manufacturers. This shows that under the principle of dynamic clearing, even if the supply chain can be partially restored, the overall operation is full of uncertainty. Closed-loop resumption of work not only faces the risk of "forced labor", but also cannot guarantee production efficiency. This production mode is unsustainable of.
WHO Director-General Tedros Adhanom Ghebreyesus said on September 14, "We are in the best position to end this epidemic. We have not ended the epidemic, but the time to end the epidemic is near." At the inflection point of 2019, China's paranoia about dynamic reset is causing long-term and far-reaching damage to the economy and society. Even if part of the supply chain resumes work and production, uncertainty still exists, and the production efficiency is not high and the cost is not low, which will weaken China's traditional role as the world's factory. The driving force for growth. On the other hand, extreme anti-epidemic policies have led to the unemployment or downgrade of a large number of young migrant workers. The deterioration of working conditions and the increase in income inequality not only pose the risk of labor conflicts and social unrest, but also fundamentally damage spending power and willingness. Promoting common prosperity is not good news, nor is it conducive to the transformation of power for economic growth.
Like my work? Don't forget to support and clap, let me know that you are with me on the road of creation. Keep this enthusiasm together!
- Author
- More