理想化
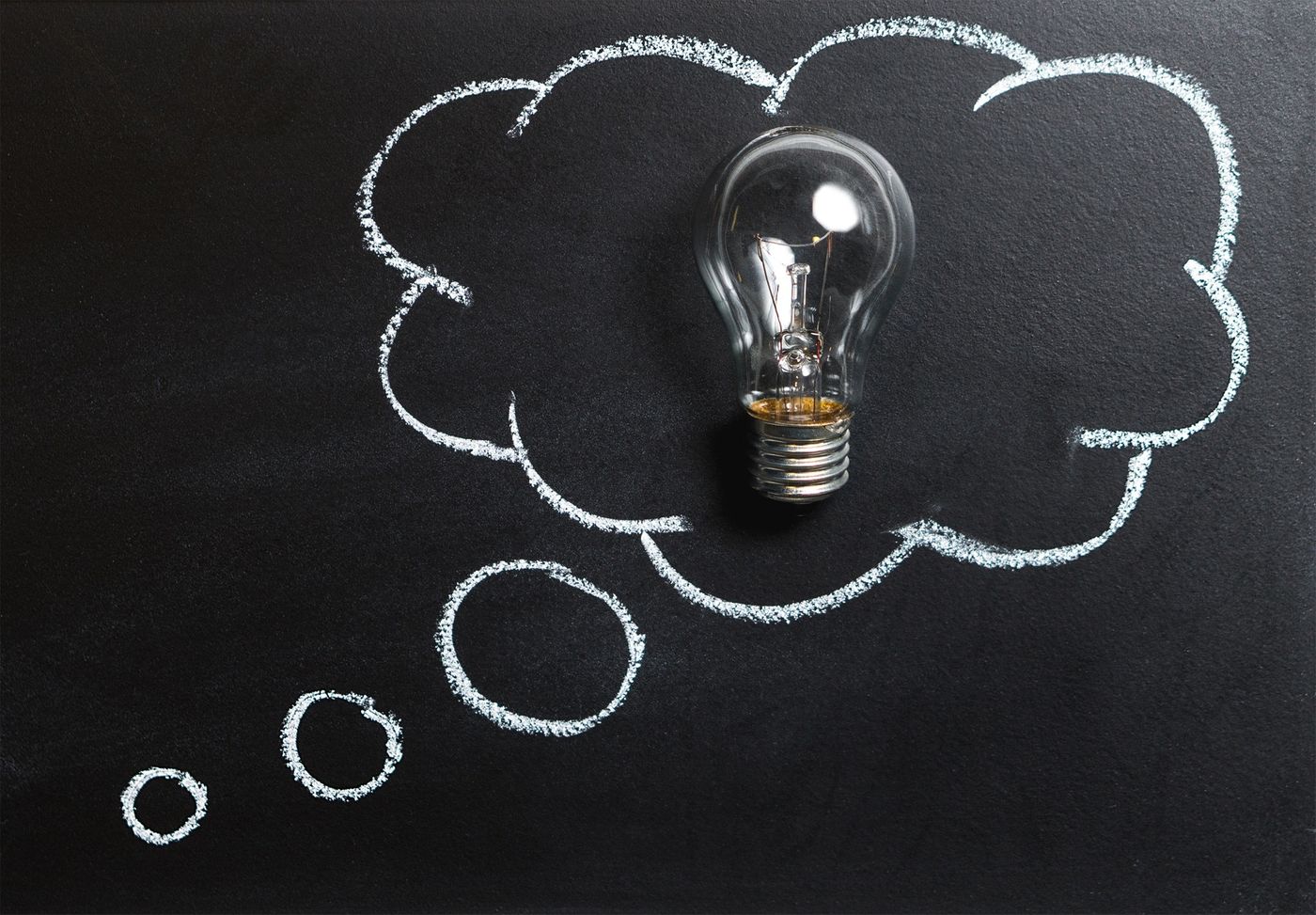
“經理,您說的有點太理想化了。”廠務其中一位有超過12年織造經歷的副理,又再抵抗將流程標準化的作業。筆者笑著回答“郭兄,如果連一點理想都沒有,公司還有改變的希望嗎?”
2012年中,初任海外中國子公司廠務主管沒多久,對於工廠的流程與管制作業,雖有一定程度的了解,但相較於底下經歷超過10-15年的中幹,現場的“人機物法環”,我還嫩的很。會在進公司不到半年的時間,就接下200多人的半自動化紡織廠,實為“蜀中無大將,廖化當先鋒”,公司恰在Adidas, Nike等歐美大廠供應鏈大舉轉到東南亞,訂單銳減,管理問題逐漸浮現之際,兩位分屬前端製程與後段製程的台籍經理人,先後因私領域問題,只能返台任職。老闆在不得已下,將廠務部門整合為一,讓筆者有機會試煉廠長一職。
因出貨量大減,固定成本率就大幅提升,而為了降低總成本,不使公司虧損,變動成本率就變成管理的重點。降低變動成本率的重點即在直接人工,直接材料與變動的製造費用。影響成本的核心因子為製程各階段的耗損率(直接可計算材料,人工及機器工時),每個階段的耗損率,則可視為每個階段產出品的不良率,因此管理真正的重點在於"品質"。
連續製程的管理,猶如一條多元的線性方程式(趨近),製程中每個階段,都看似一獨立,但實際上卻存在相互依存關係的X,每個X中,又受到許多操作及控制變因影響,此概念化的思維是受過管理碩士訓練的我,唯一的優勢。品質絕對是台商掛在嘴邊,最自豪的口號,當然公司內部每週必進行品質會議及交期會議,近半年來,也聽了不下20次的品質會議。但總發覺開會是沒有意義的,解決的是面子之爭的問題,或恃持自身的經驗,僅解決了眼前的問題,控制變因一改變,品質問題又將重複出現,甚至上回處理的方法,又改變其他控制變因,讓問題的原因又更難研判。
筆者試著將這樣的概念,講述給課長級別以上的幹部,並宣示將針對特殊的品質事件,採取找出問題後,將流程“標準化”的決心。其實執行上,也沒這麼困難,工廠內八成以上的問題,是管理的問題,非技術(設備或材料的物理極限)層面的問題,管理的問題是系統性的問題,系統的問題,在於解決非常態的統計問題,非常態事件的出現,透過一連串分析流程後,可找出容易產生變異的動作,再針對此設計SOP,根本的解決問題本質。
一開始並非進行的很順利,多數現場出身的主管,認為“太過理想化”。筆者只好更貼近現場,品質問題出現後,多諮詢問題產生點的上下游,甚至越洋向台灣母公司技術主管請益。可以發現,多數現場員工或技術前輩,皆樂於分享他們經驗,甚至表示終於有人關注這個問題了。所以即便專業不足,也可掌握到需要改變的關鍵。原本那些看不起我年輕且無經驗的主管,只好被迫面對錯誤,並開始設計新的SOP。“理想化”漸漸的不在被提起,配合BSC導入,改善的績效逐漸顯現,半年後,整體耗損率降了約30%改善了成本結構,也將改善成果財務績效,部分回饋予現場的員工,雖然業績少了近三成,但年底不至於赤字。
“過於理想化”或許是不願面對錯誤的藉口,或是畏懼改變的理由。提醒現在及未來的我,時時勿忘初衷,並由衷感謝品質改善大師今井正明先生。
本文於2015/6/27發表於過客閱讀筆記部落格。